In today’s fast-changing industrial world, the convergence of digital twins and robotics in the industrial metaverse is changing manufacturing and operational processes. This convergence offers unprecedented opportunities for design innovation, predictive maintenance and operational optimisation.
What are Digital Twins
A digital twin is a virtual replica of a physical entity, a machine, a system or a process. This digital copy mirrors the real-world object in real-time, allowing continuous monitoring, simulation and analysis. The concept has evolved a lot, it’s applied in many industries, manufacturing, healthcare, urban planning. In manufacturing, digital twins allow the creation of virtual models of production facilities and simulation and optimise processes before physical implementation.
In robotics, digital twins replicate robotic systems in virtual environments, a place to test and refine designs without the need for physical prototypes. This involves creating detailed virtual models that simulate the behaviour and interactions of robotic systems in different conditions. For example, in the automotive industry, digital twins are used to simulate robotic assembly lines, so manufacturers can optimise workflows and identify potential issues before they happen.
Digital twins allow virtual prototyping and testing, reducing time and costs associated with physical prototyping. Engineers can simulate different design scenarios, assess performance and make informed decisions early in the development process. This speeds up innovation and ensures the final product meets the requirements. For example, aerospace companies use digital twins to design and test robotic systems for aircraft assembly, resulting in more efficient production.
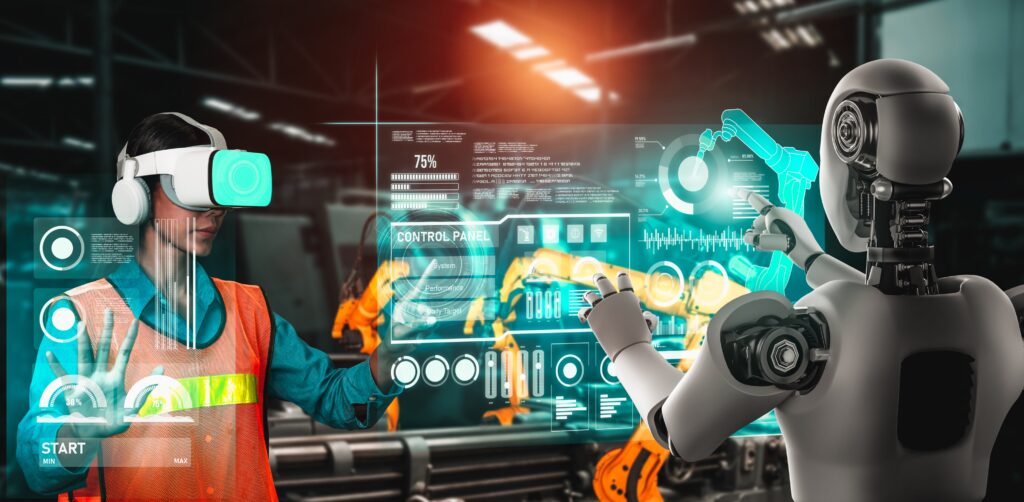
Maintenance and Predictive Analytics
By providing real time monitoring digital twins enable predictive maintenance. Analyzing data from the digital twin allows for the detection of anomalies early, and maintenance teams can address issues before they become system failures. This proactive approach reduces downtime and extends the life of robotic equipment. In the energy sector, digital twins monitor robotic systems used in offshore drilling, predicting maintenance needs and preventing costly breakdowns.
Digital twins streamline robotic operations by simulating different scenarios and optimising performance parameters. They improve human-robot collaboration by providing a virtual platform where operators can interact with robotic systems, test procedures and train without impacting actual operations. This leads to better safety, productivity and user experience. In logistics, digital twins simulate warehouse robotics, and optimise routes and workflows to increase efficiency.
Despite the advantages, digital twins with robotics has its challenges, technical complexities, data security concerns and high initial investment. Data accuracy and cybersecurity is key to successful digital twins. And the cost of developing and maintaining digital twin systems is high, so ROI analysis is necessary.
Future Trends and Developments
AI, machine learning and IoT will further improve digital twins. The industrial metaverse will see more advanced simulations, real time data integration and broader applications across industries. For example, augmented reality with digital twins will allow operators to see robotic systems in real time, better decision making and operational efficiency.
Conclusion
Digital twins and robotics in the industrial metaverse is changing industries by improving design, enabling predictive maintenance and optimising operations. As technology moves forward, we need to get on board with these innovations if we want to stay ahead in the game.